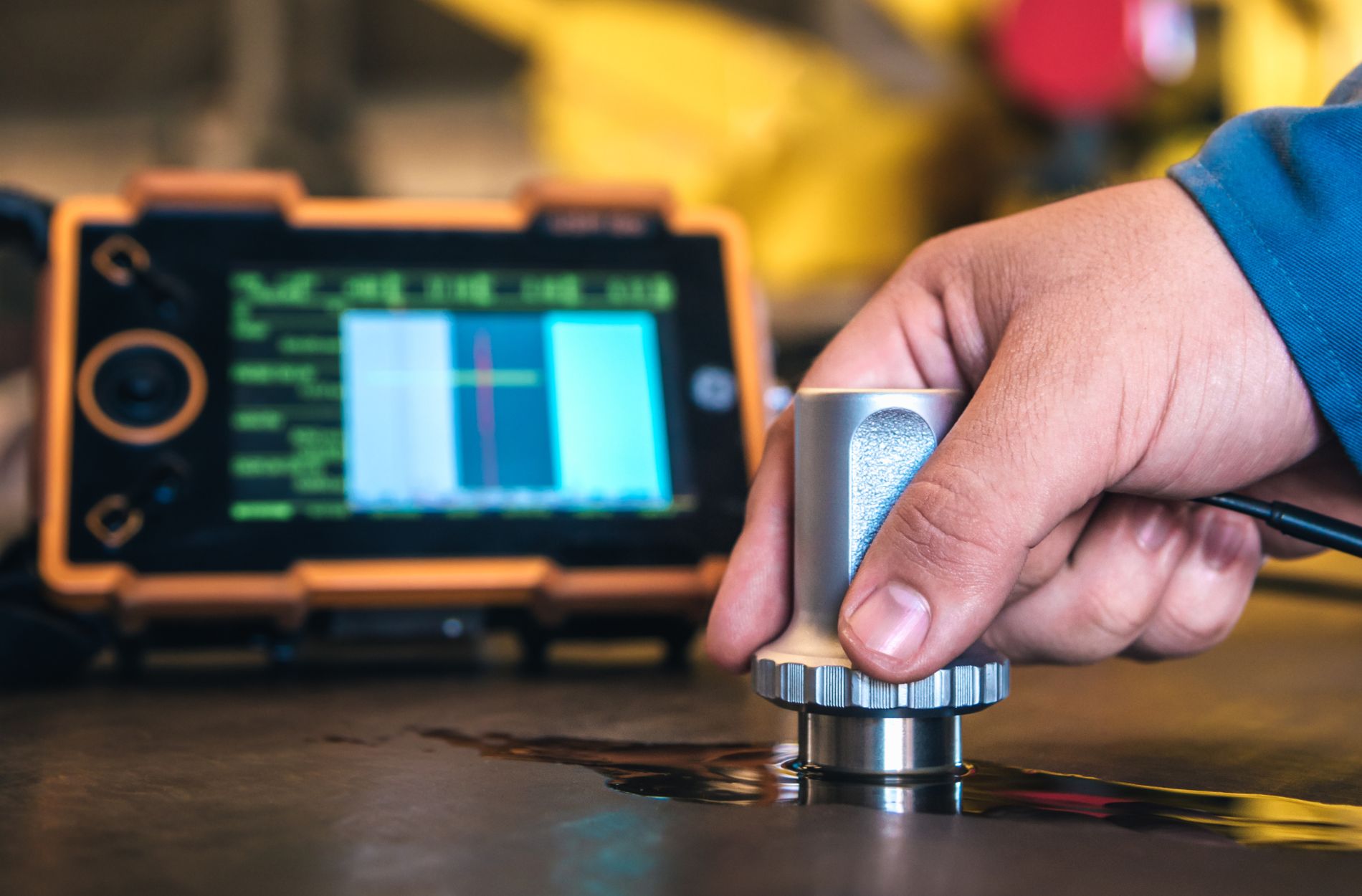
The energy industry plays a critical role in powering modern society, from electricity supply to transportation. Ensuring the safety, efficiency, and reliability of power generation plants and associated infrastructure is essential for delivering uninterrupted energy resources to communities across the globe. Nondestructive testing (NDT) technologies provide invaluable insights into the condition of power generation equipment and systems, helping to prevent failures, reduce downtime, and maintain compliance with ever-evolving safety standards.
In this in-depth and informative article, we will explore the vital role of nondestructive testing technologies in the energy industry, focusing on power generation plants such as nuclear, fossil fuel, wind, and solar. We will discuss the most common NDT methods and applications utilized to optimize plant operation and ensure the dependability of energy production facilities.
Key NDT Techniques for the Energy Industry
Maintaining the structural integrity and efficient performance of power generation plants is of utmost importance to the energy industry. Various nondestructive testing techniques are utilized to assess equipment components and infrastructure, ensuring their compliance with safety standards. Key NDT methods employed in the energy industry include:
Visual Inspection
Visual Inspection is the most basic yet essential NDT technique, allowing technicians to detect external defects and abnormalities in a variety of power plant components. These inspections may range from simple, unaided examinations to the use of advanced tools like borescopes or remote camera systems for inaccessible areas. Visual inspection plays a crucial role in assessing the condition of turbines, pipelines, heat exchangers, and other critical elements of power plants.
Radiographic Testing (RT)
Radiographic Testing involves the use of X-ray or gamma radiation to generate images, displaying the internal structure of power plant components and revealing potential defects like corrosion, cracks, or material inconsistencies. In the energy industry, RT is widely employed for inspecting turbine blades, welds, valves, and other high-pressure components, as it can provide valuable insights into areas that are difficult to access using other NDT methods.
Ultrasonic Testing (UT)
Ultrasonic Testing employs high-frequency sound waves to detect flaws in various materials, from surface to subsurface anomalies. UT is particularly useful in the energy industry due to its versatility and sensitivity, as it can be used for inspecting a wide range of components, such as pipelines, pressure vessels, tanks, and heat exchangers. The precision and speed of UT make it well-suited for the demanding requirements of power generation plants.
Eddy Current Testing (ECT)
Eddy Current Testing is a popular NDT method for detecting surface and near-surface defects in conductive materials, such as the walls of heat exchangers or steam generator tubes in nuclear power plants. ECT provides accurate information regarding material properties, allowing for the identification of defects like cracks or corrosion in various power generation equipment components, including turbine blades and fuel rods.
Advancing Renewable Energy with NDT
As the global energy landscape shifts toward renewable sources, nondestructive testing plays a vital role in ensuring the effective performance of renewable energy generation technologies, including wind turbines and solar panels. NDT methods used in renewable energy applications include:
– Visual Inspection: Examining the exterior of wind turbine blades and solar panels for signs of material degradation or damages.
– Vibration Analysis: Assessing the vibrations produced by rotating components in wind turbines to ensure optimal performance.
– Thermal Imaging: Identifying hotspots on solar panels that could indicate defects or inefficiencies.
NDT’s Role in Nuclear Power Plant Safety
Nuclear power plants operate under strict safety regulations due to the high-risk nature of their operation. Nondestructive testing plays a vital role in maintaining nuclear power plant safety and reliability, including:
– Inspection of pressure vessels and containment structures: NDT technicians perform regular inspections of reactor pressure vessels and containment structures to detect flaws or defects that could compromise plant safety.
– Monitoring reactor components: Advanced NDT techniques, such as phased array ultrasonic testing and eddy current testing, are used to monitor critical components within nuclear reactors, identifying potential issues before they become critical hazards.
– Compliance with safety regulations: NDT professionals are responsible for ensuring that nuclear power plants maintain compliance with industry standards and regulatory requirements, such as those set forth by the Nuclear Regulatory Commission (NRC).
Building a Career in NDT for the Energy Industry
As the demand for safe, reliable, and sustainable energy production continues to grow, so do the career opportunities for NDT professionals in the energy sector. To succeed in this specialized field, individuals should consider pursuing NDT training programs tailored to the unique requirements and challenges of the energy industry. By focusing on applicable NDT methods and acquiring industry-specific knowledge, aspiring NDT technicians can position themselves for rewarding and lucrative careers in a sector that underpins modern society’s infrastructure and operations.
Propel Your NDT Career for the Energy Industry with National Inspection
With a solid understanding of the critical role nondestructive testing plays in the energy sector, you are prepared to pursue specialized training that will set you on the path to a successful and impactful career. National Inspection’s comprehensive range of NDT training programs provides aspiring professionals with the skills and knowledge necessary to excel in this demanding yet rewarding field.
Embrace the challenges and opportunities of a career in NDT for the energy industry by partnering with National Inspection and embarking on a journey to propel the future of sustainable and reliable power generation.