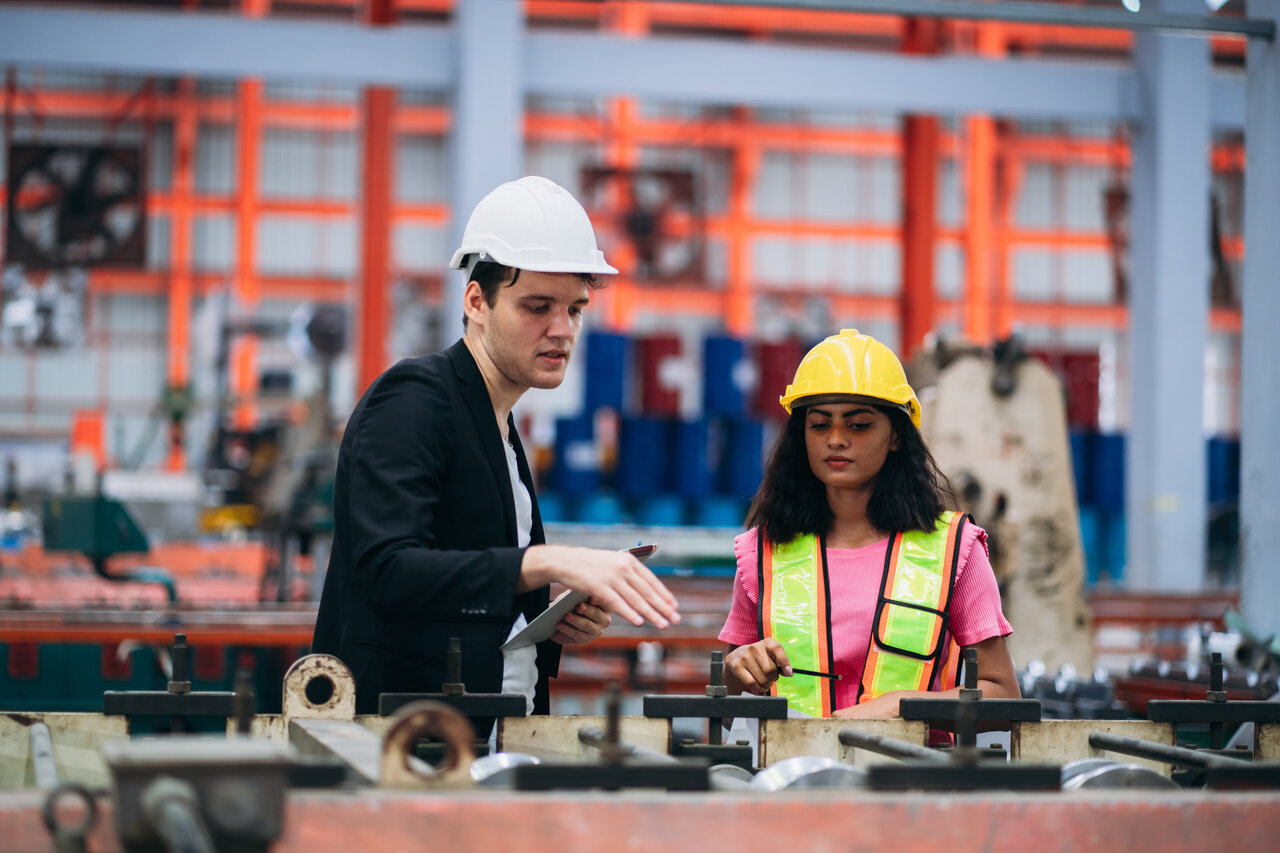
From aerospace and automotive to medical devices and construction, the widespread adoption of additive manufacturing has paved the way for cutting-edge innovation throughout various sectors of the manufacturing industry. Additive manufacturing, also known as 3D printing, provides immense opportunities for efficiencies, cost-saving processes, and customized designs. However, with these revolutionary advancements come unique challenges, particularly when it comes to ensuring the quality, safety, and reliability of the parts and components being produced. That’s where nondestructive testing (NDT) comes in, proving to be an invaluable partner in the additive manufacturing revolution.
In this article, we will delve into the intersection of NDT and additive manufacturing, exploring how the synergy of these two fields is transforming quality control and enhancing production efficiency throughout the manufacturing sector. We will discuss the unique challenges and opportunities presented by additive manufacturing, analyzing how varied NDT methods are utilized to ensure the quality and reliability of 3D-printed parts during the entire production process, including material selection, fabrication, and post-processing. Furthermore, we will examine how embracing NDT techniques can contribute to cost reduction and overall process optimization in additive manufacturing.
As an aspiring NDT professional, a strong foundation in specialized training and certifications can open the door to a wealth of opportunities in cutting-edge industries such as additive manufacturing. With our best-in-class, comprehensive training programs, you’ll be equipped with the skills, knowledge, and certifications needed to thrive in this rapidly evolving market and help shape the future of quality control and efficiency in the world of manufacturing.
Begin your journey at the forefront of the additive manufacturing revolution by embarking on a rewarding career path in NDT, and prepare to make a significant impact on the future of the manufacturing industry. Your adventure starts here.
Challenges and Opportunities in Additive Manufacturing
The rapid advancements in additive manufacturing present numerous challenges and opportunities for quality control and production efficiency. Some of the unique aspects of this technology include:
– Material Selection and Quality
In additive manufacturing processes, raw materials are critical for ensuring the quality and durability of the final product. Ensuring that materials are consistently high quality and free from defects is vital for successful production. NDT methods can play a crucial role in assessing the quality of materials before they enter the production process.
– Layer-by-Layer Fabrication
Since additive manufacturing builds parts layer-by-layer, flaws can be introduced at any stage of the production process. Monitoring these layers is crucial in detecting any issues early on to minimize waste and correct course as needed. Here, NDT techniques can be extremely valuable in monitoring the printing process in real-time.
– Post-Processing and Inspection
Once a part has been printed, it may require additional refinement through post-processing, such as heat treatments, polishing, or supports removal. Assessing the effects of these processes on the part’s integrity is crucial for ensuring quality and safety. Again, NDT methods can aid in making informed decisions.
NDT Techniques for Additive Manufacturing
As an NDT professional, you’ll need to be well-versed in a wide range of testing methods to be effective in the additive manufacturing sphere. Some of the most commonly used NDT techniques in this industry include:
– X-Ray Computed Tomography (CT)
X-ray computed tomography is an indispensable tool for additive manufacturing as it provides high-resolution images of complex internal structures. This allows for the detection of defects, such as porosity or inclusions, that may be hidden within printed parts. CT is also a beneficial tool for validating intricate geometries and ensuring dimensional accuracy.
– Ultrasonic Testing (UT)
Ultrasonic testing is another valuable NDT method for additive manufacturing, which uses high-frequency sound waves to assess a part’s internal structure. This technique is particularly suitable for metal and polymer components, as it enables the detection of flaws, such as voids and cracks, that may have formed during the printing process.
– Eddy Current Testing (ECT)
Eddy current testing is an effective NDT technique for evaluating the surface and subsurface conductivity changes in conductive materials, such as metals. This method is useful in additive manufacturing for detecting defects like cracks and variations in material properties that may compromise the part’s performance.
– Visual Inspection (VI)
While more advanced techniques are often required to assess internal features, visual inspection remains crucial for identifying surface-level issues like overhangs, warping, and residual support material in printed parts. Visual inspection should be used in conjunction with other NDT methods to ensure a comprehensive evaluation of quality.
Benefits of Incorporating NDT in Additive Manufacturing
By embracing NDT techniques in additive manufacturing, companies can expect numerous benefits, including:
– Improved Quality Control
NDT methods enable extensive, real-time monitoring during the production process, allowing for immediate detection of defects or irregularities. This enables companies to take corrective action quickly, resulting in fewer scrapped parts and less waste.
– Enhanced Production Efficiency
The use of NDT techniques can streamline the entire production cycle, from raw material evaluation to post-processing inspections. By identifying defects early on and eliminating the need for time-consuming destructive testing, NDT can significantly reduce production time and resources required.
– Cost Reduction
By detecting problems early and preventing defective parts from reaching customers, NDT can help companies avoid costly recalls and maintain their reputation for delivering high-quality products, ultimately leading to saved costs and increased revenue.
Preparing for a Future in NDT and Additive Manufacturing
As the additive manufacturing sector continues to expand and revolutionize various industries, NDT professionals with specialized training and certifications will be in high demand to ensure quality control and production efficiency. Comprehensive training programs, such as ours, can equip you with the knowledge and skills necessary to excel in this cutting-edge field.
Embark on Your Journey at the Intersection of NDT and Additive Manufacturing
By pursuing a career in NDT focused on additive manufacturing, you’ll not only have the opportunity to contribute to the advancement of technological innovation but also help to enhance the quality and performance of essential components across multiple industries. By starting your journey with National Inspection Academy’s comprehensive NDT training programs, you will be well-prepared to make a significant impact on the future of the manufacturing sector.
Take the first step towards a rewarding and impactful career in NDT for additive manufacturing by embarking on your path to success with us, and let’s shape the future of quality control and production efficiency together.