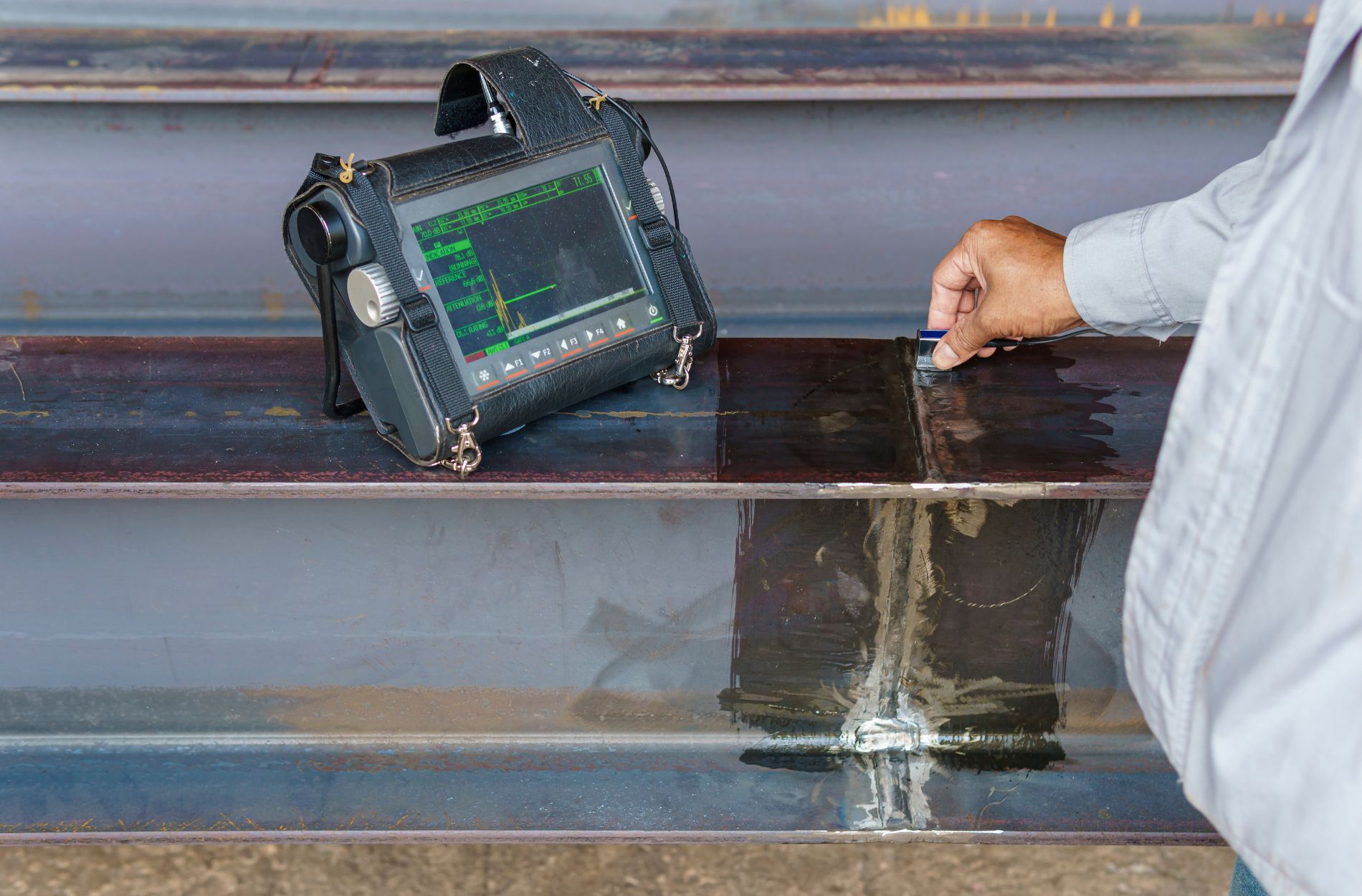
Nondestructive testing (NDT) encompasses a diverse range of methods and techniques aimed at evaluating the integrity, properties, and safety of materials or components without causing damage or altering their functionality. As an NDT professional, mastering the core methods and understanding their applications is crucial in providing accurate assessments and ensuring the highest level of safety across various industries.
This guide serves as an invaluable resource for both aspiring and seasoned NDT technicians, delving into the fundamental nondestructive testing techniques, their underlying principles, and areas of application. We explore NDT methods like ultrasonic testing (UT), radiographic testing (RT), magnetic particle testing (MT), liquid penetrant testing (PT), and many more, providing a complete landscape of the NDT domain.
Sharpen your expertise and expand your capabilities by immersing yourself in our extensive guide to NDT techniques, unlocking the power of nondestructive testing to maintain safety and quality in your chosen field. Embrace the opportunity to elevate your career and knowledge with this essential guide to the world of nondestructive testing.
Ultrasonic Testing (UT)
Ultrasonic testing (UT) is a widely used NDT technique that employs high-frequency sound waves to inspect materials for internal defects, measure thickness, and identify potential failure points. UT is a versatile method applicable to various materials, including metals, plastics, and composites across industries such as aerospace, automotive, and oil and gas.
UT involves emitting ultrasonic waves into the material, which then reflect off internal defects and return to the transducer. The time it takes for these reflections to reach the transducer is proportional to the depth of the defect. By analyzing these reflections, NDT technicians can determine the presence, location, and size of defects within a material.
Two common types of UT include straight beam (used for thickness measurements and defect detection) and angle beam (used to locate and size defects such as cracks and weld anomalies). Due to its non-hazardous nature, speed, and precision, UT is an invaluable technique in many industries.
Radiographic Testing (RT)
Radiographic testing (RT) is a well-established NDT method that involves the use of ionizing radiation (X-rays or gamma rays) to inspect materials for internal defects and hidden discontinuities. RT is suitable for various materials, including metals, ceramics, and plastics, and is commonly used in industries such as aerospace, pipeline inspection, and casting production.
In RT, X-ray or gamma-ray sources are placed on one side of the object, while a detector (film or digital device) is positioned on the opposite side. Defects in the material appear as differences in density on the image, allowing NDT technicians to identify the presence and location of internal discontinuities.
Although RT can provide high-resolution images and has been trusted for decades, it comes with some drawbacks, such as potential health risks due to ionizing radiation exposure and the need for strict safety measures.
Magnetic Particle Testing (MT)
Magnetic particle testing (MT) is an NDT method specifically designed to detect surface and near-surface discontinuities in ferromagnetic materials. MT is widely used for inspecting welds, castings, and forgings across industries such as automotive, aerospace, and power generation.
The MT process involves magnetizing the material (either locally or overall) and applying ferromagnetic particles (dry or wet) to the surface. If there are discontinuities, magnetic flux leakage occurs, which attracts the particles and forms visible indications on the surface. NDT technicians can then visually inspect these indications to determine the presence, location, and nature of defects in the material.
MT is fast, low-cost, and easy to apply, making it an attractive option for detecting surface defects in ferromagnetic materials. However, it cannot be used on non-magnetic materials and is limited to detecting only surface and near-surface discontinuities.
Liquid Penetrant Testing (PT)
Liquid penetrant testing (PT), also known as dye penetrant testing, is an NDT method that detects surface-breaking defects in non-porous materials, including metals, ceramics, and plastics. PT is commonly used for inspecting castings, welds, and forgings across a broad range of industries.
PT involves applying a liquid penetrant (visible or fluorescent) to the surface of the component. The penetrant seeps into open surface flaws, and after a dwell time, the excess penetrant is removed, leaving behind only the penetrant trapped in the defects. A developer is then applied, which draws the penetrant out of the flaws, creating an observable indication on the surface. NDT technicians can visually inspect these indications to identify the presence, location, and size of surface defects.
PT is widely applicable, cost-effective, and provides rapid results. However, it is limited to detecting surface-breaking discontinuities and requires a thorough cleaning of the component both before and after the inspection.
Eddy Current Testing (ECT)
Eddy current testing (ECT) is an electromagnetic NDT method that evaluates the integrity of conductive materials (mostly metals) and detects surface and near-surface defects. ECT is often used in industries like aerospace, automotive, and nuclear power plants for inspecting heat exchanger tubes, aircraft structures, and automotive components.
ECT involves inducing an alternating current into a coil that generates an alternating magnetic field. This magnetic field induces eddy currents in the test material, which create their magnetic field. The interaction between the material’s magnetic field and the coil’s magnetic field is measured, allowing NDT technicians to detect changes in electrical conductivity and magnetic permeability that indicate defects in the material.
ECT has advantages such as speed, portability, and the ability to inspect complex shapes and sizes. However, it may be limited by variations in material properties, lifting-off effects, and depth of penetration, requiring trained professionals for accurate results.
Empower Your NDT Career with National Inspection Academy’s Comprehensive Services
Mastering the core nondestructive testing techniques is essential to truly excel in your chosen field and ensure the safety and quality of the materials and components you inspect. By understanding the principles and applications of these diverse NDT methods, you equip yourself with the knowledge and expertise needed to tackle the challenges that arise across various industries.
At National Inspection Academy, we are dedicated to providing in-depth training, guidance, and support to aspiring and experienced NDT technicians, helping you develop and refine the skills necessary for a successful career. With our commitment to quality, safety, and technical excellence, you can trust that our tailored NDT services will offer the ideal foundation for your professional growth.
Unlock your full potential in the dynamic world of nondestructive testing with NDT training in Baxter offered by National Inspection Academy. Discover our comprehensive range of NDT training programs and services designed to equip you with knowledge and hands-on experience. Invest in yourself and enhance your NDT expertise with National Inspection Academy by your side.