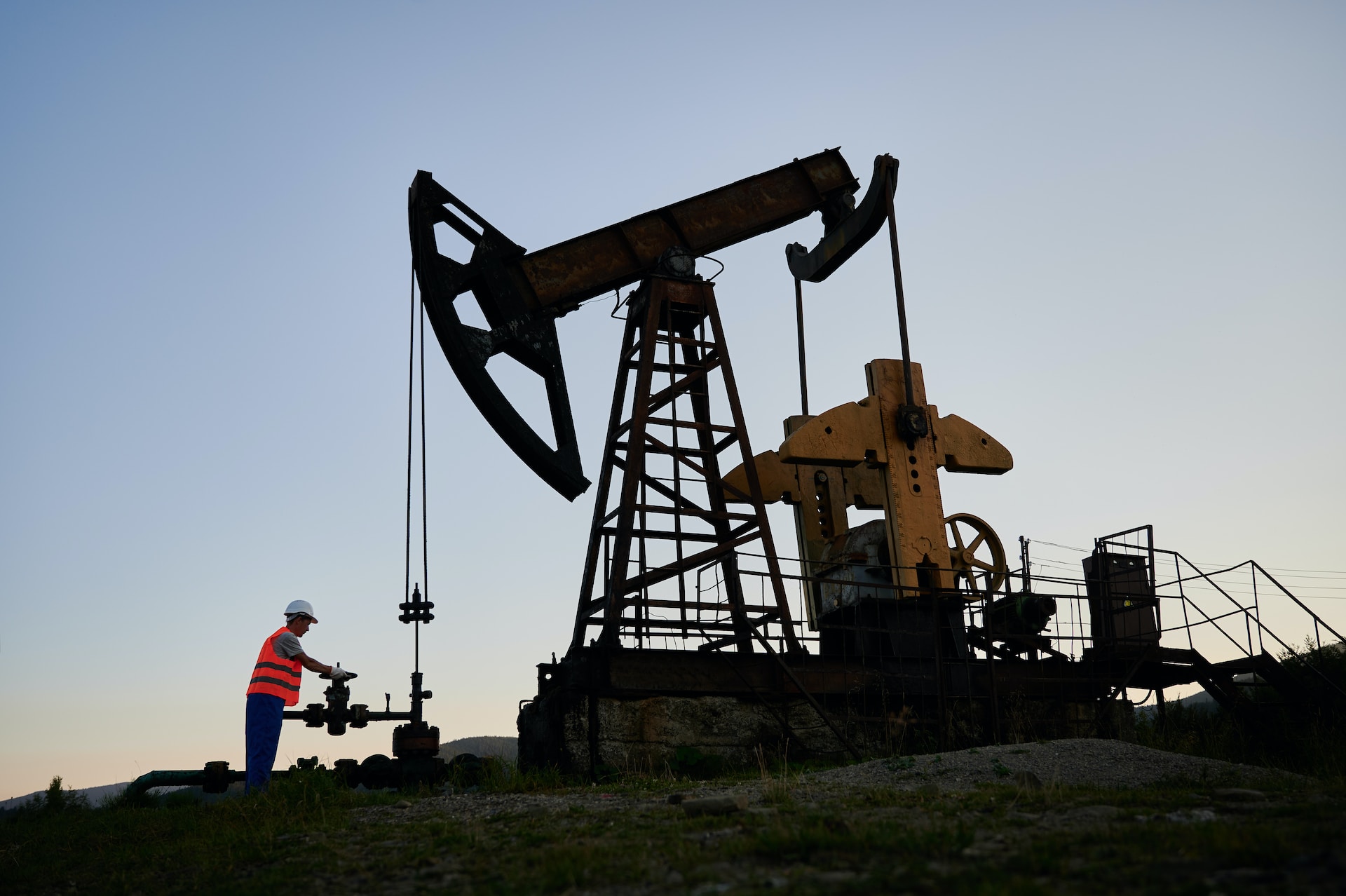
The world of nondestructive testing (NDT) offers a multitude of techniques and methods designed to detect flaws, evaluate materials, and assess the quality of various components without causing damage. As an essential aspect of industries such as construction, aerospace, and manufacturing, understanding the fundamentals of NDT techniques is critical for those looking to excel in this competitive field.
In this comprehensive guide, we will explore the core methods of nondestructive testing, diving deep into their applications and advantages in various industries. You will gain valuable insight into key NDT concepts, such as visual inspection, ultrasonic testing, magnetic particle testing, and more. Learning about these techniques will not only enhance your knowledge but also help you better appreciate the art and science behind nondestructive testing.
Stay tuned as we embark on a journey to uncover the secrets of NDT techniques and how they contribute to the safety, reliability, and efficiency of countless industries all around the world. This informative guide will provide you with the foundation you need to harness the power of nondestructive testing and propel your career to new heights.
Understanding the Core Methods of Nondestructive Testing
Nondestructive testing techniques are broadly classified into several categories depending on the principle they operate on and the specific application they serve. Let’s analyze these core methods and the situations in which they work best.
Visual Inspection (VT)
Visual inspection is the most fundamental and widely-used NDT technique. It involves the direct observation of a part, structure, or system using the naked eye or optical aids such as magnifiers, endoscopes, and borescopes. Visual inspection is crucial for detecting defects like corrosion, cracks, or leaks, as well as assessing compliance with predetermined specifications.
Some advantages of visual inspection include low cost, fast results, and minimal training requirements. However, it has its limitations, as it can only detect surface defects and is often subject to human judgment errors. Thus, visual inspection is usually supplemented with other, more sophisticated NDT techniques.
Ultrasonic Testing (UT)
Ultrasonic testing uses high-frequency sound waves to penetrate materials, detecting both surface and subsurface flaws. This method involves transmitting a sound wave through the material, which then reflects off internal imperfections or the opposite surface. By measuring the time elapsed between the transmission and receipt of the sound wave, technicians can locate defects and determine their size and orientation.
Common applications for ultrasonic testing include weld inspection, crack detection, and wall thickness measurement. UT is highly effective for materials like metals, plastics, and composites. However, it may be less effective for porous substances or materials with irregular shapes.
Magnetic Particle Testing (MT)
Magnetic particle testing detects surface or near-surface defects in ferromagnetic materials. This technique works by magnetizing the test component and applying a magnetic powder suspension. Any discontinuities in the material will disturb the magnetic field, causing the particles to cluster around the defect, forming a visible indication.
Widely used in industries such as automotive, aerospace, and construction, MT is highly sensitive to minute defects. Its primary limitation is that it only works for ferromagnetic materials, making it unsuitable for non-magnetic materials like aluminum or austenitic stainless steel.
Liquid Penetrant Testing (PT)
Liquid penetrant testing is a cost-effective technique used to detect surface-connected flaws in non-porous materials. The process involves applying a liquid penetrant (usually a bright-colored fluorescent or visible dye) to the part’s surface, allowing it to seep into any faults present. After a specific period, the excess penetrant is removed, and a developer is applied, which reveals the defect by drawing the entrapped penetrant back to the surface.
PT is widely employed in industries such as aerospace and automotive and is particularly useful for non-magnetic materials. Limitations of PT include its inability to detect subsurface flaws and contamination risks if not performed correctly.
Applications of Nondestructive Testing in Various Industries
NDT techniques serve a variety of applications in numerous industries, ensuring safety, quality, and reliability. Here are a few industries that rely heavily on NDT methods:
Aerospace
In the aerospace sector, NDT is vital for ensuring the safety and integrity of aircraft components and structures. Techniques such as radiographic testing (RT) and eddy current testing (ECT) are utilized to inspect engine parts, turbine blades, and other critical components for defects, fatigue, and cracks that could pose significant hazards if undetected.
Oil and Gas
The oil and gas industry relies on advanced NDT techniques for the inspection and monitoring of pipelines, storage tanks, and pressure vessels. NDT methods such as guided wave ultrasonic testing (GWUT) and acoustic emission testing (AE) allow for the early detection of corrosion, leaks, and material degradation, reducing the risk of environmental contamination and costly failures.
Power Generation
In the power generation industry, NDT plays an essential role in the inspection and maintenance of critical infrastructure such as nuclear reactors, boilers, and turbine components. Techniques like phased array ultrasonic testing (PAUT), radiographic testing (RT), and infrared thermography (IR) are employed to detect material defects, thermal anomalies, and other issues that could lead to catastrophic failure and downtime.
Transportation
NDT is also crucial in the transportation industry, ensuring the safety and reliability of railroads, bridges, and other structures. Methods like eddy current testing (ECT) and magnetic flux leakage (MFL) are employed to assess metal structures for corrosion, cracks, and other material defects, safeguarding against potential accidents and failures.
In conclusion, nondestructive testing techniques play a pivotal role across numerous sectors, safeguarding lives and property and ensuring quality and reliability. By understanding the core NDT methods and their applications, professionals can harness the power of these techniques, leading to safer, more efficient, and more resilient industries.
Embrace the Power of NDT: Boost Your Career and Create a Safer Future
The world of nondestructive testing is brimming with potential, offering innovative solutions to safeguard lives and maintain the integrity of vital structures in numerous industries. As an NDT professional, understanding the core methods and their multifaceted applications is integral to your success and the future of various sectors. With the right knowledge and tools, you can excel in your chosen career path, creating a safer and more efficient world for all.
At the National Inspection Academy, we are passionate about advancing the field of nondestructive testing (NDT) and fostering a highly skilled and certified workforce. Our comprehensive NDT training program, offered in partnership with trusted institutions, equips you with the knowledge and skills needed to thrive in this dynamic field. Trust our certified Level II and Level III inspectors to guide you through your professional journey, ensuring the highest standards are upheld in every step.
Now is the time to invest in your career and contribute to a safer and more resilient future through the power of nondestructive testing. To learn more about our NDT training program or explore our wide range of NDT services, visit our website today. Empower yourself with the expertise required to unlock your full potential and become a standout professional in this highly competitive field.