Magnetic Flux Testing
The primary application of magnetic flux leakage testing (MFL) is ferromagnetic materials, including tubing, plate, wire, oilfield tubulars, and pipelines. In the petrochemical world, MFL is used predominantly for tank floor inspection. The power source is provided by permanent magnets or DC or AC coils. MFL has been extensively used in the pipe inspection industry. This entails the introduction of a moving DC magnetic field into a ferromagnetic test piece. Any localized, normally surface breaking discontinuities that lie within the inspection zone will cause the field to bend or leak and extend above the surface at that point. These flux lines cut across a moving coil or sensor and are used to detect the leakage field. In many piping and tubing tests, MFL is used to look for general corrosion. The locally thinned area puts a higher magnetic flux distribution in the space nearer to the flux detection device. This relative increase in field strength can be measured. MFL performs best with the detection of volumetric discontinuities rather than small pits or cracks. Pipeline inspections are performed with what are called smart pigs. These devices can carry out multiple nondestructive tests simultaneously. However, the most common test performed is MFL. Large inspection pigs use MFL in order to detect internal or external corrosion. The flux leakage may be detected by hall effect probes or passive induction coils.
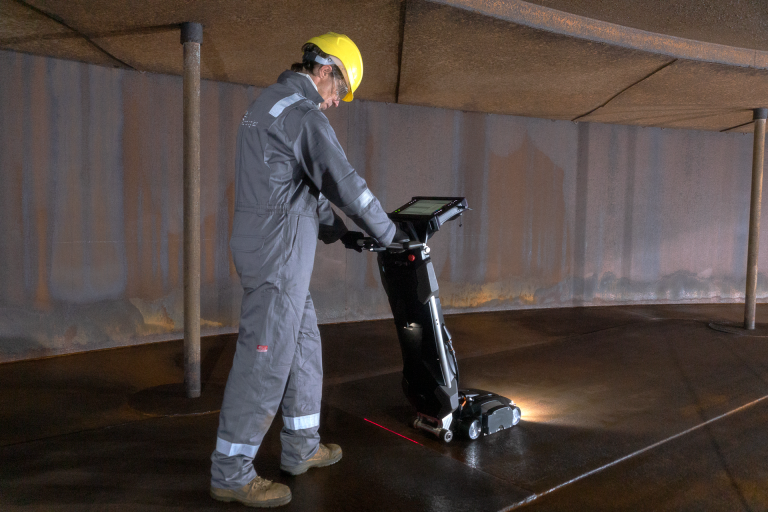
Magnetic Flux Leakage Testing (MFL) Course:
This is a 24-hour course which satisfies the training hours needed for Level I and II certification in accordance with SNT-TC-1A and ANSI/ASNT CP-189.
Please call for scheduling before completing purchase of course. 218-851-8347